A cast silver cup from a 3D-printed wax model
It is a process with a lot of craftsmanship and handiwork
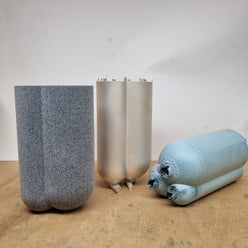
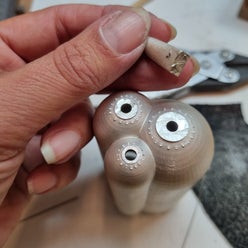
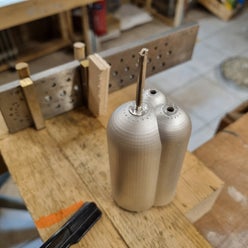
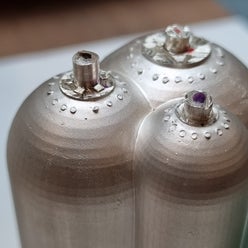
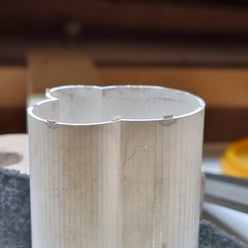
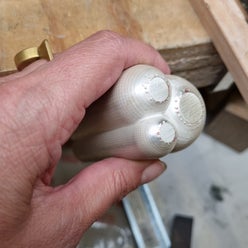
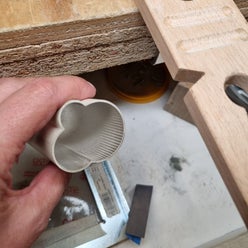
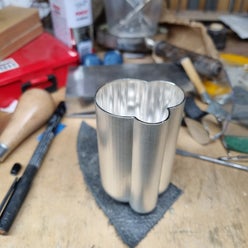
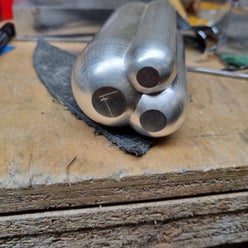
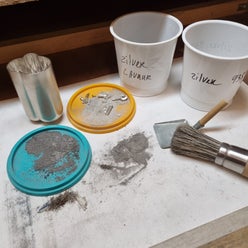
It's often thought that a 3D printer gives a ready-made end product. There are some materials where this is true. An example is the grey sample in the photo. You can also print silver directly, but that is still very expensive. Therefore, only the wax model is 3D printed. A 3D computer model can be more complicated than a hand-formed design. The casting process and finishing remain the same. A 3D print also has limitations. For instance, holes were made in the bottom of this cup to print it. The 3D print is created in a bath of liquid wax and resin. The mix solidifies at the spot where laser beams cross, forming the shape. This liquid mix must flow away, allowing the form to harden under the influence of UV light. In a cup without holes in the bottom, the liquid remains. As a result, you would get a block instead of a hollow shape. This cup's shape and thin wall make casting it technically complicated. Therefore, two wax models were printed so I could show the blue spare model. The technical support and craftsmanship of Horbach's casters from Idar-Oberstein made my idea a reality. On the bottom and the rim, you can see the casting channels at the silver cup. The second picture shows
me holding a sawed-off casting channel in my hand. With a drawing iron and the drawing bench, I transform the casting channel into a round wire that I can use to fill the holes. (Photo 3) For each gap, a fitting rod is made. Around the left-hand rod, there are already solder chips. (photo 4) These are pieces of silver solder. Once the cup is made red hot with a burner, the solder melts. Then, the cup is watertight, and the excess material at the top and bottom is filed off afterwards. The inner side is sanded and polished; the outside is given a satin sheen. Finally, I engraved the letter F by hand. I aim to produce as sustainably as possible. Therefore, I only make a plastic proof print if necessary. While working, I carefully separated the waste. I can remelt filings and sawn-off castings and use them myself. Sanding debris contains a relatively large amount of silver. I keep it separate from the leftover sandpaper, polishing residue and other waste. This way, it can be recycled more efficiently, as, unfortunately, recycling also costs energy.